Whenever you have a high quality shirt made by a bespoke shirtmaker or MTM manufacturer, chances are you will choose between fabrics from the Albini Group, which consists of Cotonificio Albini, Thomas Mason, David & John Anderson and Albiate 1830.
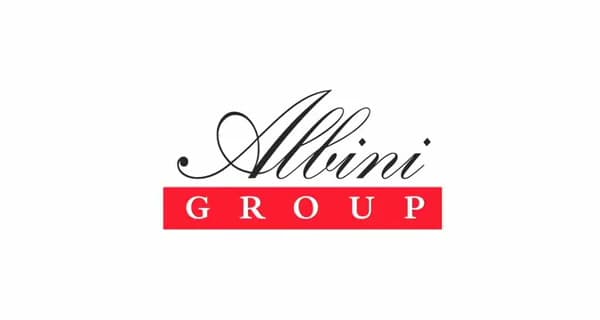
Albini History
Originally, the company was founded in Desenzano sul Serio near Bergamo, Italy in 1876 by Zaffiro Borgomanero. Initially, the company was named Z. Borgomanero & C, and after just a year of operations, Zaffiro had already acquired 40 mechanical looms which were operated by 44 employees. Eight years later, they received the bronze medal at the Industrial Exhibition in Turin. In 1890, the childless owner decides to pass on the company to his nephew Giovanni Albini. By then, the weaving operation had grown to include 107 looms and 90 staff. As the head of the Bergamo Chamber of Commerce, Giovanni Albini became increasingly important in the area. Shortly after WWI, the company was broken up and passed on to Giovanni’s children Riccardo and Silvio. The latter changed his portion of the business to the name to Società Dr Silvio Albini & C.It is unknown what happened to the other half of the company. Throughout the economic crisis of the 30’s and WWII, Albini managed to stay afloat and remained in family control. By 1968, the fourth generation of Albinis – Gianni, Giancarlo, and Marino – are in charge of the company. In 1984, Silvio Albini became responsible for the business and under his leadership, the company quickly expanded into foreign markets. Silvio’s
new ventures proved to be very successful, and in 1991 Albini considered a take over of the British shirt fabric producers Thomas Mason and David & John Anderson. The deal went through in 1992, and the two brands are added to the Albini Group portfolio. In 2000, Albini continued its acquisition spree by taking over Albiate 1830 Milano. Over the next few years, finishing plants outside of the company grounds become part of the group, like Manifattura di Albiate that has two plants in the Czech Republic and one in Italy. Recently, a logistics center was added, which enables the company to offer more than 20,000 fabrics!
Albini Today
With such an impressive array of shirt fabrics, Albini has become a major player for shirting fabrics in all three major markets: high end bespoke, made to measure and ready to wear. Zegna and J.Crew have some of their shirt fabrics made there, alongside numerous other businesses of varying size and quality. The current line of products incorporates a large quality range starting with sporty, casual and denim fabrics, to British inspired high quality fabrics of the Thomas Mason, Silverline, Goldine and seasonal lines, all the way up to the most expensive fabrics which are produced under the David & John Anderson Label. Moreover, they also offer RTW, MTM and bespoke shirt services in house.
One of the things that makes Albini so successful is their well-managed vertical integration strategy. They eliminated the middlemen by controlling all the important elements of the business, including everything from the growing the cotton to creating the yarn, weaving, dying, shrinking, distributing and now even shirt manufacturing. In addition, they were able to acquire more than 700 historic swatch books from Thomas Mason and D&JA, enabling them to create new but historically influenced designs. Paired with state of the art machinery, there is probably nothing in the world of shirting fabric Albini would be incapable of producing.
Personally, I own a number of Albini winter and summer fabrics and so far they have all performed very well.
In the following,you can watch an interesting video showing how Albini fabric is sourced, made and sold:
How Shirt Fabric Is Made
Video Recap:
First, it starts with the production of a yarn, introducing the machinery and emphasizing the importance raw materials and testing facilities, because every yarn is different. Only after it is ensured that the yarn is consistent enough, it is tested for strength, twist and stretch, to guarantee a smooth weaving process. Next in line is color and color testing. Subsequently, it is explained how the the weaving process is prepared and executed.
Next up is the finishing process: first the fabric undergoes gassing, also known as singeing, which is a process producing an even surface by burning off excess fibers, and fuzz. This result is achieved by running the fabric at high speed over a gas flame allowing the unwanted material to burn off without burning or scorching the fabric.
For the next 36 h, the fabric is emerged and kept in a cold bleach. The subsequent hot bleaching removes impurities and restores the colors to their original tone.
Once this step is completed, the fabrics are mercerized. Mercerization is named after its inventor John Mercer and it gives the fabric a beautiful luster as well as more strength by altering the chemical structure of cotton. Basically, this treatment causes the cell wall of the cotton fibre to swell, creating a larger surface area and hence better reflectance and softer feel. In order to improve this effect, the cotton fabric is often immersed into a sodium hydroxide solution and subsequently neutralized in an acid bath. This process increases the reflections and luster even more, especially on long staple cotton.
Once dyed for 48h hours, the fabric is ready for the final finishing processes. Here, the fabric is soften and brightened in a special machine before it is subject to calendaring, a mechanical application of pressure which makes the fabric softer.
During sanforization, the weft is compacted and the warp is stabilized. Sanforized fabrics are desirable because ideally, they prevent any shrinkage from washing afterwards.
In order to obtain special effects such as peach skin washed out effects, some fabrics are then sanded, softened or treated in different ways.
Finally, the fabric undergoes quality control once more – visually and at the lab. Once if passed all the steps, the fabrics is packed and stored in Albini’s logistics center from where it is delivered all around the globe.
The following three videos are a little more detailed than the one before but they contain many of the same sequences.
Very impressive … thank you
Thank you for the video. That was very interesting.
I am glad you liked it Sajeel and J. Posey.
Great video…. I have one shirt from Hackett made by Thomas Mason.Really good quality …