In our third installment of my bespoke shoe journey with St. Paul, Minnesota shoemaker Amara Hark Weber, we discuss a very important step of the bespoke shoemaking process, where you will, at last, know what a last is and how it is made.
What Is A Last?
Basically, a last is the thing you build a shoe around. It is modeled after the human foot, not an exact copy. For a ready-to-wear-made factory shoe, typically, the lasts are made out of plastic. It also comes in many different sizes, so you can just make the shoes.
For a bespoke shoe, the individual measurements of your foot are taken into consideration, your stylistic choices, and a pair of lasts created that is unique to your foot. It’s important to note that the last is not a replica of your foot. Trust me; I have five toes on each foot, not one massive chisel.
Rather, it’s a model to fit and shape your shoe. So, while it may be sized to a particular foot, it looks more like a shoe than a foot. Also, no human being has identically mirrored feet. Instead, they’re all slightly different. Some may be longer or thicker, wider or slimmer. Even if they look the same visually, I bet you they’re not.
With the last, you have the ability to create more symmetry and maybe shape them in a way that both look more alike than your feet do. Also, if you have multiple types of bespoke shoes made, typically, you have different lasts.
For example, if you have an Oxford or a derby, you can use the same last if you don’t want to change the toe shape. If you want to change the toe shape, you’ll make a different last.

Also, let’s say you want to keep the toe shape but you want to switch from an Oxford to a loafer, you will also create a new last. With a loafer, everything has to fit a little tighter because there are no laces that keep the shoe on your foot. Likewise, if you have a pair of ankle boots or full boots, you need different lasts to make the shoe around.
A quality last will ensure that you have something that fits you that is comfortable and stands the test of time. So, it’s a very important step in the bespoke shoemaking process.
Creating The Last
It’s important to keep in mind that different shoemakers can make lasts in very different ways. We’ll take a look at how Amara Hark Weber did her last and see what we can learn about lasts from her.
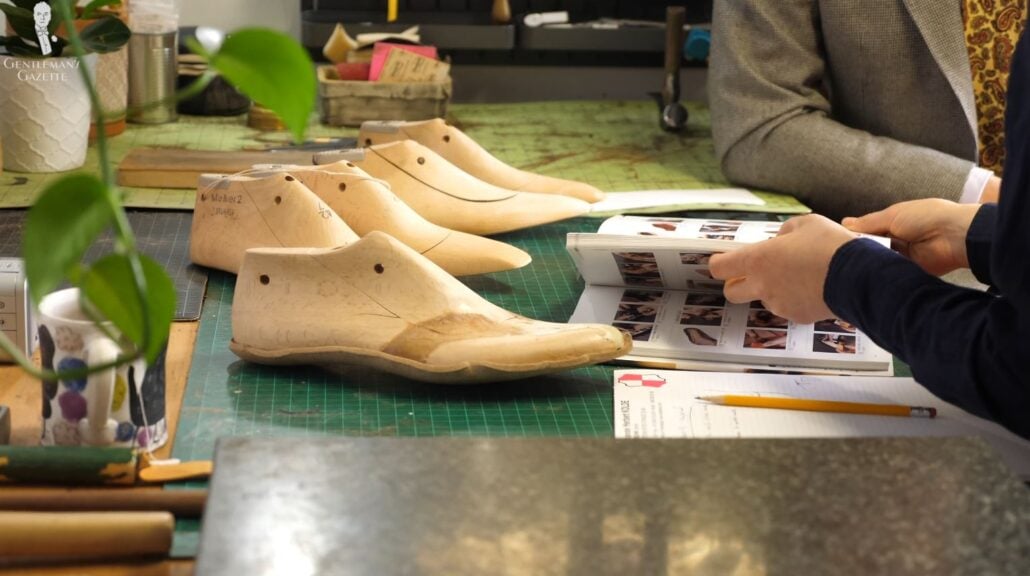
Sourcing the Last
First of all, you have to source the last material. Typically, it’s made of wood, but what kind of wood depends on the companies you work with. A last has to be a sturdy thing. Why? Well, it’ll get wet, see nails, get hammered on, get sanded, and it just has to stand the test of time. It’s very important for a last to maintain its shape. Otherwise, the final shoe will be compromised.
I’m sure some bespoke shoemakers work with something other than wood, but mostly that’s what you see today. Typically, a block of wood is carved down for each client. If you have a boot tree, for example, that block needs to be separable. Otherwise, you wouldn’t be able to get the last out of the shoe once your final boot is done.

For shoes, a last can be a one-piece thing, or it can also be cut into multiple things that is then screwed together. What matters is that there are no moving parts, and that the shape remains exactly the same.
Most shoemakers I’ve encountered start with a blank last. Meaning that it’s not a block but it’s something that resembles a final last pretty closely. From that blank last, the shoemaker, then, either carves down or sands down the material or they build up with other materials, such as leather, for example, or cork, or epoxy.
Modifying a Blank Last
Amara uses blanks because it’s much more cost-efficient. She used to buy a vintage shoe last, would modify them, then have new base lasts made based on the desired look she wanted.
When I asked Amara Hark Weber about it, she said that she appreciated the romantic part of the craft of carving down a block of wood into a last, but that, for her at her price point, which is comparatively low, it simply didn’t make sense. And personally, I’d rather pay less for a bespoke shoe and get exactly the last I want from a base last, than paying for someone to just do woodwork by hand that can be done much faster by machine.

During the bespeaking process, which you can watch here, we decided on a blank last, and now had to be modified to fit my measurements, as well as my stylistic ideas. Your shoemaker should be able to explain to you the logic behind what they do and why they do it.
Of course, my experience was much more in-depth because typically, a customer is not around when a shoemaker makes the last. If you’re interested, you may always ask; maybe they’re open to it, maybe they’re not. Who knows?
In my case, I wanted narrower, more elegant lines that were more extreme on my last. I wanted a chiseled toe and a much slimmer waist. In addition to stylistic choices, the desired fit can also impact the decision on carving down or building up a last.
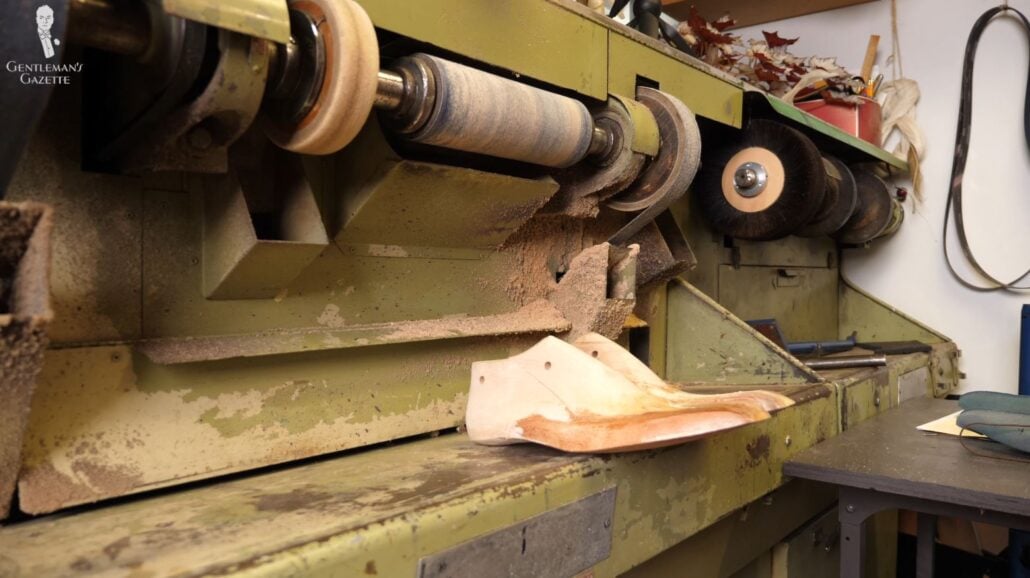
Amara also had different base last sizes, so she could decide what she felt was best in each particular case. Initially, I shared with her that I thought what I wanted was a rather tight fit. Of course, the fit is highly subjective, and she shared a story with me of two customers.
There were two pairs that I was building at the same time, and one was a pair for someone who was a speed skater, and so he was used to his feet being really snug inside a shoe. The other person was a classical musician, and he liked a lot of room.
And so, as I was building both of these pairs of shoes, one I kept getting smaller and smaller with the fit models, and one got larger and larger with the fit models…I almost felt like I was losing my mind!
But, at the end of the day, the measurements of the final last were very different than the measurements of their feet, because what they needed in their shoe was, was a different feel, and neither of them was quite what I would be able to anticipate.
Amara Hark Weber
Naturally, if there’s no reference point, the shoemaker has to listen. If you already have an example of something that you like, it’s great to bring it in, put on a shoe, and say, “I like this, or I dislike that. I want a little more room here or there.” That just gives me an understanding of where you want to go.
By no means is that necessary, though, and some shoemakers may even not want to do that because they don’t want to be subject to undue influence.

In my case, Amara thought it was better to build up the last than to shave it down. She also prefers to use leather to build up a last rather than cork because she feels it can take more of a beating, and is not as flexible. That being said, she still uses cork in areas where it won’t make a difference because it’s easier and faster to work with.
Other core materials used to build up a last blank are Bondo, which is a body filler material used in the car industry, or Apoxie Sculpt, which is an adhesive product that has to dry first and can then be sanded off. The good thing is they dry to a very hard durable form, but that takes time. Because of that, Amara generally avoids those. But each to his own.

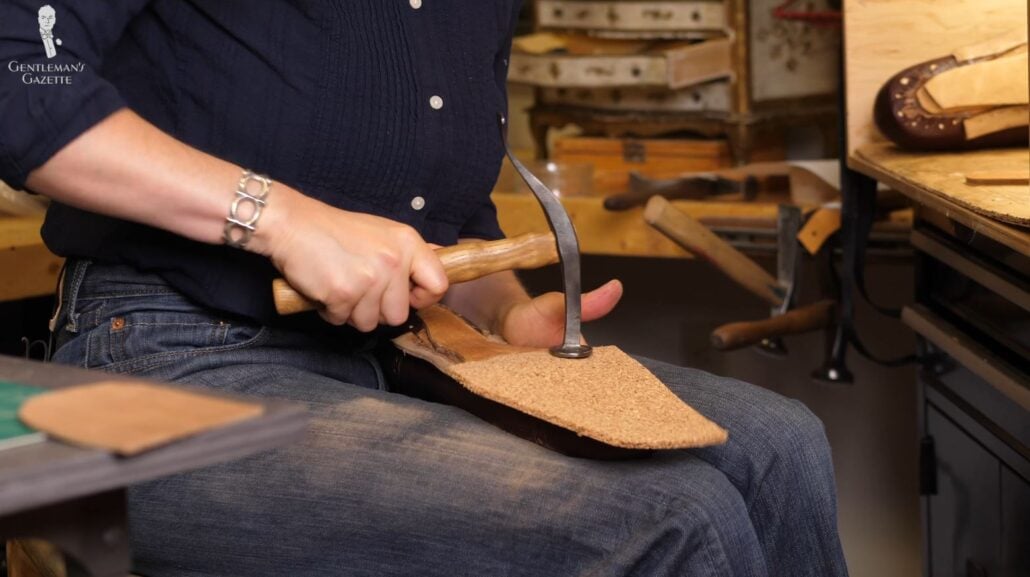
She decided to use a leather for the toe area because that’s how she likes to work. But, ultimately, your shoemaker will have their way of handling things. No matter what materials a shoemaker uses, the goal is always the same – creating a last that works for your foot and looks the part.
So, how do you build a last with leather? Well, first of all, the leather has to be wet. Having wet leather makes it easier to shape to the existing last. To make sure it stays on there, it’s tacked into place, and while it dries, it molds itself perfectly onto that wooden surface.
Shaving Down a Built-Up Last
After the leather has dried, it has to be cut and then shaved off to be part of the last. Typically, there are two ways to do that. One is to use a rasp and shave it down by hand, the other is to use a machine. I’m sure your shoemaker will have their own preference. Amara prefers the machine because it is faster and always very precise for her. Specifically, Amara uses a finishing machine that has a grinder with sandpaper on it.
While being a lot faster than doing it by hand, it also puts less strain on her body. Yes, shoemaking is exhausting, sometimes dangerous, and literally backbreaking. So, personally, I appreciate using tools and where possible getting a better result in a faster time while protecting the craftsman or craftswoman behind it. After all, I want Amara to have a long career so I can come back for more shoes.

Of course, Amara also has a rasp, and she uses it for some finishing work, but she doesn’t use it exclusively. Personally, I care about the result, and I want the craftsman to be comfortable with the process and confident because, if they lack that, chances are the final result is not what I want.
I would advise you never to pressure your shoemaker into doing certain things all by hand or in a way they’re not comfortable with because that’s just not the recipe for a great outcome.
What are the next steps in the last-making process? The leather that has been tacked onto the last and has dried now has to be marked in place; the tacks have to be removed. Otherwise, in the finishing machine, they would wear differently than the leather.

So, how does leather stay in place? Well, it’s glued. Of course, this is where all sorts of different, interesting, and obscure tools come in that I have never seen. For example, to remove the tags, you use a tack puller. That’s a scary-looking instrument, and I thought the ones at my dentist’s office looked scary.
Once the tacks are out, she glues the leather on with a product called Renia, which is from Germany – just like I am. It’s a contact cement that glues everything, including PVC, according to the instructions in the bottle. It’s stinky.
This tight-bonding rubber cement will completely affix those leather layers to the last. Like many industrial glues, it’s really not a wise idea to inhale all those fumes, and so Amara’s partner built her a little chamber that would suck out all those fumes.

And just like that pedograph, it seems like he’s really handy and can help her build customized products for her craft. Pretty cool, if you ask me.
To ensure a proper fit of the leather, they’re carefully placed but then also hammered so no lines are disrupted that would compromise the final look of the shoe. You can see Amara is always carefully watching, measuring, looking, and making sure that everything fits right to a millimeter.
Getting to Work
Applying the Build-Ups
Once everything is in place, it’s time to start shaping the last and the leather on the finishing machine. The main job here is to get the last to a point where the fit is good. Also, we want attractive lines and toe shapes because what good is a shoe that fits well but looks ugly?
After all, a bespoke shoe ideally will stay on your foot without laces. So, when the laces are there, it doesn’t have to be too tight, and it’s comfortable wearing a shoe all day.

Because of that, it’s not just about the individual measurements but also about the curves and how the final shoe will hug your foot. As Amara is working on shaving down the last, she’s very careful not to take off too much because fixing it would mean the entire process of last making would take quite a bit longer.
Using Measurements Constantly
For that reason, you’ll see that she constantly uses her measurements, the pedograph, and her notes to see if what she’s doing aligns with the foot. She can take all the sensitivities, your bones, your sensitive areas into consideration that way. Also, if you have a slim and bony foot, she may make different decisions on the last design as if you have more of a fleshy foot.
Of course, the measurements provide exact dimensions. But, as an artist, she also has to keep the looks in mind. Think of it like a marriage. It takes compromise. I’ve been married for a few years, and that’s very much the case.

The pedograph offers more precise information about the largest part in the foot, and so, Amara is constantly referencing it. Why? Well, the pedograph shows how the shape of the foot changes as weight is applied to it versus if you just sit. Of course, the shoe must be comfortable when you sit and walk or even run.
The shoemaker never wants that the shoes are too short, of course, or too long, but the key is also that you have two shoes and two lasts that look the same. Honestly, every shoemaker will have a different way of applying measurements to the last, and whatever it is that they find works for them is fine. What matters is the result.
Looking At The Tiny Details
As she continues to work, Amara makes it look very easy, but it requires a lot of concentration and experience, and skill. Amara largely taught herself last making, so it’s a mix of intuition, trial and error, and influx from other shoemakers and last makers.
Of course, in between, she also takes care of her machinery, so sometimes you’ll see her using some rubber on the machine.
Here you can see her going over the last with her fingers, so she uses them like eyes to see if there are any bumps and how the curves actually feels in her fingers.

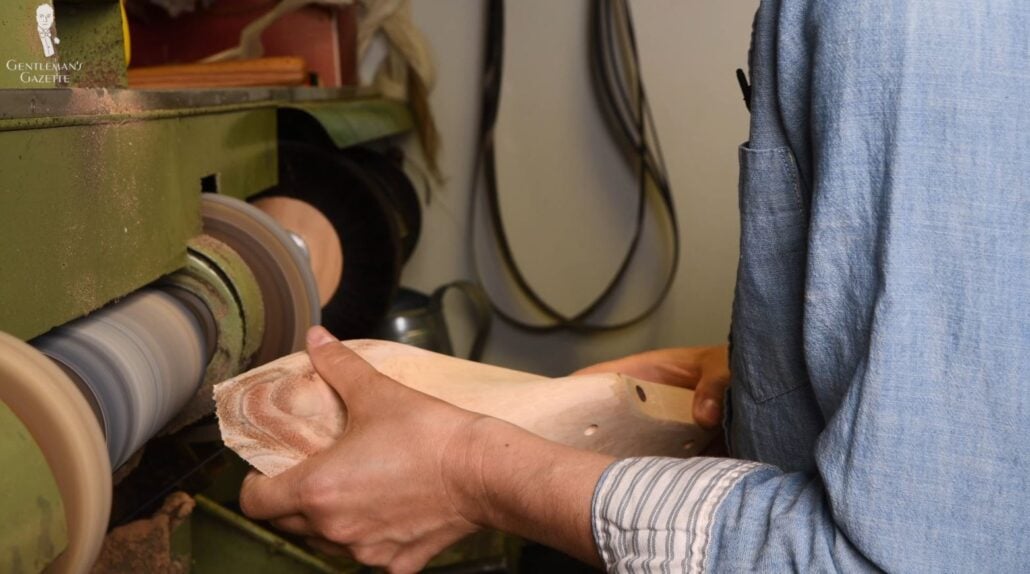
Speaking of tiny details, here we can see Amara working on the toe area. Remember how big and bulky that looked when it started out? With the finishing machine, Amara has curved down to a pleasing organic curve. She neatly and seamlessly is integrating into a last, so the shape mirrors what we had discussed.
Personally, I found that point really exciting because I could see the exact shape the last would take and if I liked it or not. I really appreciated being there because you can give instant feedback if, of course, the shoemaker is asking for that.

Throughout the process, Amara compares the two toe shapes many, many times because, as you can imagine, it’s somewhat easier to get an excellent toe shape on one last. But, to get a matching one on the other last is a whole lot more difficult.
At this part of the process, Amara had worked on the last machine for 45 minutes. In that time frame, she went back and forth numerous times between the measurements, the pedograph, and the machine. Of course, every measurement is important – otherwise, she wouldn’t take it – but they’re all taken into consideration in different ways.
Checking and Double-Checking
Amara paid particular attention to the joint and the shape and rise of the arch. She does that because those are some of the most important for comfort and fit. Frankly, she was double checking, triple checking, and it took quite a while, but she just wanted to get it 100% right.
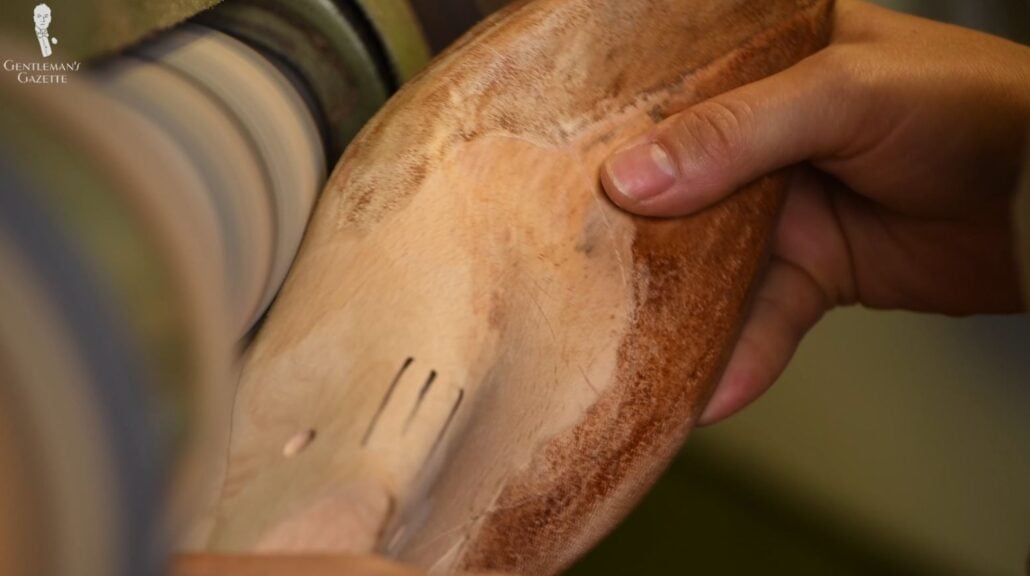
Ultimately, the more time she spends perfecting the last, the higher the likelihood that the shoe will really fit. That being said, with most shoemakers, there’s always a certain percentage where the final shoe will not be satisfactory, and it will have to be remade. Honestly, it’s hard to believe after seeing all this attention to detail, but that’s what she shared with me.
After Creating The Lasts, Shoemaking Begins
Once the last is done, the shoemaking process can start; except some shoemakers start with a trial shoe, others work right away on the real thing. Of course, there are pros and cons to both.
If you work with a trial shoe, you typically use less expensive leather, sometimes you use a cheaper glued-on heel, and you just want to get an overall idea of how it fits in the foot. Then there are some shoemakers who basically make the trial shoe from the exact same leather as the final shoe because they want to see how it feels on the foot, and it’s almost like a real shoe.
Amara, on the other hand, had more of a simple trial shoe with a heel that was just put under – it wasn’t even glued on – because she just wanted to see how it fit. She was also able to cut it open, see what it looks like from the inside, but it didn’t at all feel like the final shoe that I finally got.
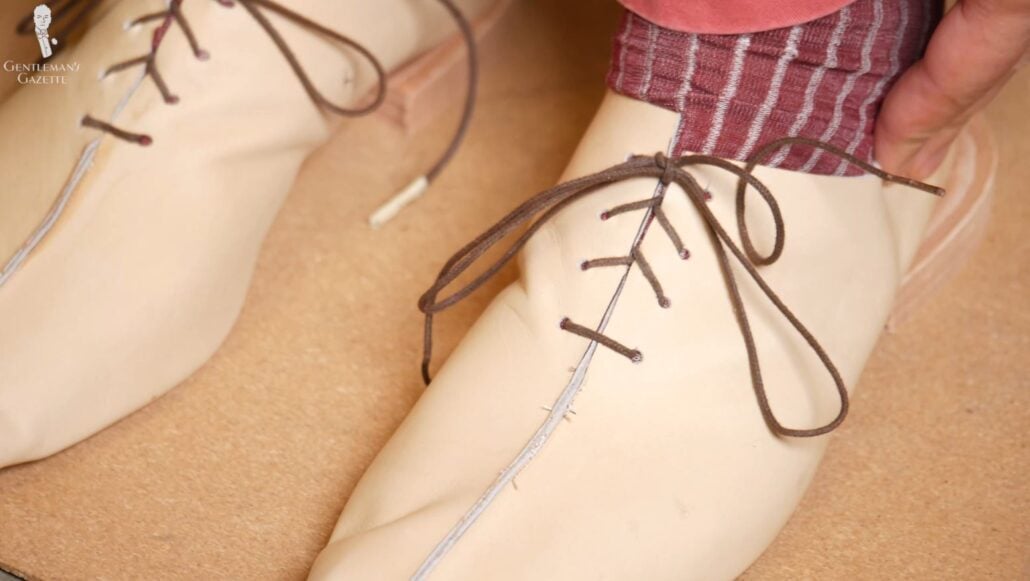
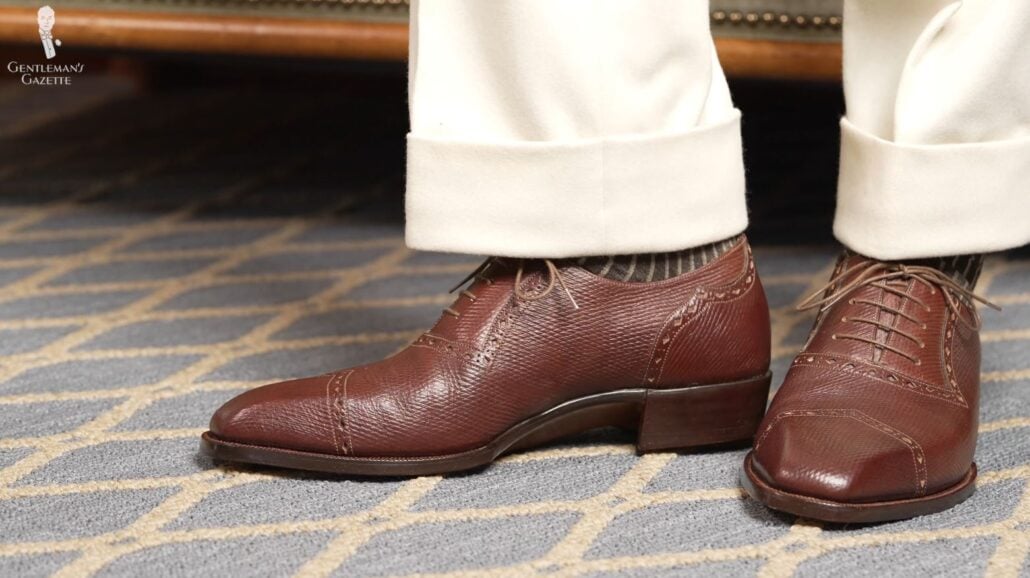
Ultimately, most shoemakers will do trial shoes to prevent having to redo a shoe at the end of the process. At the same time, if a shoemaker has to weigh up if they want to spend more time on a trial shoe or just accept that maybe one out of ten shoes has to be remade, there’s no right or wrong. And I’ve seen people who said they got better fitting shoes from shoemaker that didn’t use trial shoes than the ones they did do trial shoes. So, having a trial shoe is not a guarantee to get that perfect fit.
That being said, the likelihood of your first bespoke shoe being the absolute perfectly best fit is very low. It’s just like with a bespoke suit the very first product is really the best in terms of fit.
What kind of last would you want made for your bespoke shoes? Let us know in the comments!