As we’ve learned in our bespoke shoemaking experience, having shoes made bespoke will cost the customer time, effort, and money. But what if you could do it remotely? Yes, it is possible, and it’s less costly, too. In today’s video, we sit down with Simon Wegmann of Wayman Bespoke to discuss how they made our bespoke shoe!
Video Transcript [Lightly Edited for Clarity]
[Raphael] Welcome back to the Gentleman’s Gazette. Today, I have with me Simon Wegmann from Wayman Bespoke. Simon, pleasure to have you here.
[Simon] Thank you very much for the invitation.
[Raphael] So, we’re here in Florence at Pitti Uomo, so kind of a makeshift studio situation. But, Simon has a very interesting approach with his company where he makes remote bespoke shoes in China, but you’re in Frankfurt, Germany, right?
[Simon] That’s right, yeah.
[Raphael] So, how did you start and go down that path of making bespoke shoes in a remote way?
[Simon] So, yeah, it kind of started with me having very difficult feet. So, I’ve always had issues finding shoes off-the-rack that would kind of fit me in kind of any sensible way. So I, like once I got my first kind of job, where I needed proper leather shoes, dress shoes, I was looking around and couldn’t find anything that would fit me even remotely. So, then I kind of started looking into bespoke, but I quickly noticed that it was quite far outside of my budget. So, then, I was kind of trying to find the makers that were a bit further away, but maybe a bit lower in cost. But, they all told me like, if I wanted to get measured, I would have to go there; and then with the traveling and so on, it would be even more expensive than having something made within my reach.

Simon Wegmann
His passion for classic menswear went hand in hand with a huge interest in well-made shoes. It took him two and a half years to develop the remote bespoke shoe program. When he got sucked in deeper and deeper into the world of bespoke and handmade shoes, his expectations for the program grew with it. With a dedication to highly skilled handwork, his company was able to offer the shoes fully hand clicked, hand lasted and hand welted.
So, I kind of wondered why it wouldn’t be possible to kind of take your the measurements yourself send them to the maker and then they would make the last with maybe a trial shoe and send it to you. But, they all told me it’s impossible, you can’t do it, but I kind of couldn’t accept it. So, I reached out to a bunch of people and kind of made connections along the way and kind of was referred to different shoemakers from different people.
So, in the end, I kind of developed this remote program where you would measure your own feet, and get a trial shoe and then, the finished pair; and, along the way, I kind of figured out I put so much effort into this and I’m probably not the only one with this issue that I could probably offer it to other people as well. So, from this initial need for a proper pair of shoes for myself, this business idea grew and then, like, right before COVID started, I kind of went all out and and started the company.




[Raphael] That’s awesome, that’s awesome! It’s great! So, basically, you had an issue you wanted a solution, and you didn’t take no for an answer. You were persistent and pursued it, and then you had a product. You said you’ve difficult feet? You have a pair of shoes here, can you just hand it over so we can actually look at them? Okay, so this is a pair of shoes. I mean, the look is rather classic. Kind of walk us through the details here.
[Simon] So this is a classic cap-toe Oxford with the quarter brogue, which is like the whole punch in the front for the cap.
[Raphael] Got the swan neck here.
[Simon] Exactly, the swan neck, which is kind of like a nice design detail. Then, you have the seamless heel, which is very unique for bespoke shoes or very high-end ready-to-wear shoes; and then, what we also do is like this very close-cut heel with this pitch

[Raphael] And just to make sure, again, you know, normally, what you see would be a seam in the center back here. Basically, what you did, it’s not one piece of leather, but you still have a piece here, a piece here around, and then another piece again here. But, it’s a neater look. It’s also something I usually go for. And then, you say tight heel, you mean like here, right? There’s hardly any gap if you compare it with a factory shoe; you just get this really nice, yeah, tight heel.
And even if you look from the back here, you can see it’s very kind of tapered. That’s what you get with a bespoke product. It’s layer by layer of leather. It’s not a ready-made block.
[Simon] Exactly. The heel, you can, for our shoes, choose how much of a pitch you want. If you want it quite square or like a medium pitch, which is already a bit stronger, and then you can even go more extreme and you can also pitch the kind of inside of the heel next to the sides. And then another kind of bespoke detail is also the outsole with a very close-cut, very narrow waist


[Raphael] Yeah, and you can even like see a little bit like if we hold it like this, right? You can see the waist. It’s really slick, slim, nice, curved, and round. You can see how it’s cut in here. Typical, like, bespoke or really high-end ready-to-wear or made-to-order shoes.
[Simon] Yeah, and these are obviously also already well worn, so you can see how the waist is still kind of like intact, and I also put toe taps on on the front, which you can get done by a cobbler as well, but this is also a service we offer.
[Raphael] Like right off the bat? So, you just wear them down a lot less?
[Simon] Yeah, exactly.
[Raphael] Have you ever done the toe taps on the heel?
[Simon] Well, we have done it for like kind of our bespoke samples. But, to wear it with like a metal piece at the back is very uncomfortable because it clacks a lot and also if you go inside somewhere, you will scratch up the floor. So, usually, it’s not very practical in like everyday life, but it looks cool.

[Raphael] I’ve seen, sometimes, like, you know, someone had like almost like a little wedge, little triangle cut in there, so it would wear less or, I mean, if you put it on the rubber, you get a little bit of wear protection. But, I think the rubber works pretty well. In the toe, like you’re not screwing up the floors initially. I was worried cause we have a wooden floor. We screwed up, but it really doesn’t seem to do it much.
[Simon] Yeah, I mean it doesn’t also. I mean, it looks nice but it also doesn’t make sense for everyone to have this done. It just makes sense if you kind of wear out the front of your soles prematurely, which I, for example, do because if I don’t put these on, I will kind of almost like rub off the front of my outsole before the shoes are even worn in properly.
[Raphael] So, then, you have to kind of repair it really prematurely, and, otherwise, you walk through the welt, and then it’s a lot more expensive to fix
[Simon] Exactly, exactly.
[Raphael] Yeah, but nice! It’s like channel soles, right? They cut in so nice.

[Simon] Yeah, and what we do is kind of the outsole right here is fully stitched by hand, so you get also a very tight stitch density, much tighter than what you would find in ready-to-wear shoes.
[Raphael] So, what do we have here?
[Simon] It’s probably 10 or 11 stitches per inch.
[Raphael] Per inch? So, about one stitch every like two or so millimeters.
[Simon] Yeah, probably, yeah. And then, some design details, which you also see in bespoke shoes are like the kind of inversed v-shape for the lacing. So, once you have like a small gap up here, it looks almost parallel. The whole stitching area.
[Raphael] Yeah, and I mean, typically, over time, right, when you do a bespoke shoe, because leather’s a natural material, you start with a little gap and then, eventually, it should close as you wear it more frequently.

[Simon] True, yeah. And that’s also a question I get a lot, like from first fittings where there’s a small gap, and people are like, “Seems it’s too tight,” but actually, you want to have a small V gap right up here, so you can still kind of tighten the shoes as the leather stretches and wears in
[Raphael] Cause if you don’t, you actually have overlapping leather, so it should start like this, cause if you don’t have it and you start like this, it’s going to be like this, and it’ll look awful and you want to avoid that.
[Simon] Yeah, and it’s also like you might kind of lose the grip inside the shoes if they aren’t fitting tight enough.
[Raphael] So, I mean, you mentioned before, right, going with bespoke for you was a very personal fit thing cause you’re like… What issues did you have? The shoes were too wide for you, right, or what was the issue?


[Simon] Well, I have very strange feet overall. Like for example, my pinky toe was always pinched, but I have a lot of excess volume right here at my big toe joint, and then, I also have a very low instep.
[Raphael] That leads to wrinkles cause you have more volume or air here, you get the wrinkle here. You move around.
[Simon] Right, but even more so like when I tried on shoes ready-to-wear, I couldn’t even… Like the lacing would just overlap because I had so much space here. I couldn’t even like have… Even if I tied them down completely, I couldn’t get any grip inside the shoes. So, even the new shoe was overlapping, so there are like some workarounds like tongue pads and so on, but in the end, it really didn’t didn’t do much for me.
[Raphael] Nice, okay. All right. So, yeah, so obviously, there’s the fit aspect for bespoke, right? Another aspect that I value, too, is the customization, right? Being able to truly create something that is unique.

And then, of course, there’s also the relationship with the shoemaker. I enjoy, you know, bouncing my ideas off their experience cause it’s a cool… Oftentimes, you know, we, as a customer, like we don’t know it all, right? We think we do but then really you learn a lot. Maybe walk us through the process, and then we can talk about, like, you know, how does the fit work for you, how is the customization, and how is that kind of relationship aspect, right? Maybe let’s start with a fit process. I mean, I underwent this process myself with you and so did Preston. So, I think we started with some measurement instructions, right?
[Simon] Yes, probably usually even before that, most customers reach out to me via email or text. Just to kind of clarify some things even before they kind of start the ordering process, and then, yes, you start with the measurements. We have a website, where we kind of have all the instructions, also a short instructions video next to the paper guide, and then you kind of take the measurements yourself. Most customers send me the measurements before they place the order.


[Raphael] And it’s not even yourself. I think it’s best to have someone else doing it. Like you stand, so you need two people. But, you do that, and the nice thing is, too, like you can just take your phone these days and just like film it. You see how it works and that gives you a bit more information so you see it. Was it done properly and you know what’s happening? And, then, also, I think I shared kind of, you know, my idea, right? Like if I’m like, “Hey, I like really tight shoes or I have this toe pain here. Please, let’s consider that.”
I think, I said, let’s put a little bit of foam in there so let’s build the last so there’s enough room for a little bit of foam in there. So, if I’m at a really long day of walking, I will have no pain whatsoever, right? Cause compared to like a sneaker or a tennis shoe, if you walk all day on cobblestones, you will feel it more. I also think there’s this tendency now that people wear these like Hoka shoes with these huge foam layers and that can actually lead to foot pain, right?

There’s that fit thing, so I just communicated with you, and you were like, “Okay, we could do that.”
[Simon] Yeah, exactly, so I mean, of course, especially doing it remote, there are there are some limitations with what kind of fit issues we can accommodate because we aren’t orthopedic shoe makers so we can make a shoe that fits comfortable or comfortably and looks good, but we can’t kind of fix any issues for the feet. So, yeah. So, that’s kind of… We have to manage expectations in that regard.
[Raphael] Preston also has, similar to you, difficult feet, right? And he has one leg that is slightly shorter than the other, so you were able to accommodate all of that stuff. But, so it was nice. Then, I think the next step was you with the measurements, and then one day, I just had like a trial shoe that showed up.
[Simon] Yeah, exactly, so we take the measurements, and then we build the custom last from these measurements. What kind of differentiates us from more traditional shoemakers is that we make a 3D model of the last and have it milled out. So, this saves us a lot of money and also time compared to kind of…
[Raphael] Hand tools?
[Simon] Hand tools, and doing it from wood.
[Raphael] Okay, so it’s like a CNC machine?

[Simon] Yes, exactly. Exactly. And so, it’s a plastic last essentially, and then, yeah, so this will be the the first. You choose the toe shape for the last. We have three different ones, which kind of should be enough for everyone to choose what they like aesthetically and then, of course, the last is built on your foot measurements anyway, so every kind of shoe will look a little bit different and the toe shape will look a little bit different because of the foot width and so on
[Raphael] I remember we had a long email thread, right? It was like you have a good Instagram archive. I think in your website, you have drawings, which personally I thought weren’t that helpful cause they’re stylized, right? The style is not as the shoe will actually turn out.
It’s more like of the idea. You want a double monk strap, you want this. So, you have basic things but then, I found actually going to your Instagram or even picking up other pictures and sending them to you was really helpful in communicating. And so, I was always communicating with you.

It was always the same person. You’re obviously not the shoemaker but, at least, you know how to communicate with your shoemaker so I felt it was a good level of detail and I could express what I wanted in that shoe and also get the feedback from you. We’re like, “Well, I don’t know if we can do that or maybe that’s a bit difficult.” But, overall, I think you mentioned something of most people get, you know, an Adelaide or like a cap toe Oxford or… Tell me a little more about that.
[Simon] Yeah. So, in the beginning, when I when I first started this program, was like, all my kind of followers on social media were like shoe enthusiasts. So, people who were… loved buying shoes and doing different stuff with colors, with patterns, and designs, and so on. So, the first customers I had were all shoe enthusiasts who loved the freedom they had with designing their own model, which we also offer, can pretty much… can pretty much do anything that’s kind of within reason. And, but nowadays, of course, we still have those customers, but they’re very few, and more so like people who actually have fit issues, who kind of need a pair of shoes that fits them well, that’s probably the first pair of shoes that’s hand welted and so on. So, they go to us, and they usually go quite conservative, because…
[Raphael] Which is fine. Cost per wear, you just get more wear out of it.
The Simple Equation: Cost Per Wear
[Simon] Exactly.
[Raphael] And it’s all a good thing. So, for example, I think you know, this is the kind of shoe that we talked about, and I think, you know, it was like you had some leather samples, and you had pictures. I thought the pictures were quite small in that two-dimensional shape. I much rather like looking at them on the finished shoe.
[Simon] Yes.
[Raphael] That was really helpful, and so at first, I was like, well, maybe we can make this butterfly-style loafer and have suede here. But then I changed my mind because I was like, well, if I polish of shoes, it’s probably going to be more difficult with a suede. After all, I think it would have worked either way. But this is like that Museum calf leather and this is kind of this grained scotch grain, but it has this nice like, I would say, a darker peak and a lighter valley. So, I thought that that was really nice.


[Simon] I think we put a bit of a patina on it as well. We have like this kind of changeant effect.
[Raphael] Nice. Yeah, but the cool thing was I was like, “Well, can you do it here? And I was like, well can you do it in the back, right? Kind of to have that theme of that butterfly and I even asked Simon, “Hey can we do the stitching in like an X stitching right to kind of get that,” and you tried it but you were like, “I wasn’t happy with it.” So, then we just skipped it, right, but then here you did like a nice Vibram…
[Simon] Heel block.
[Raphael] Vibram heel block and this is a beautiful waist. It’s very tight. You have the Johannes Redenbach sole. I mean they went out of business, but I think the recipe was bought and then toe plates. So, I’ve worn them a bit, as you can see. They’re not worn extensively, but it’s, um, yeah, it’s good to see the toe shape, too. We had, I think, a round-toe shape first. And it was a bit of miscommunication, ’cause initially it was like, “Well, you can still decide on the toe shape,” and then we went down and then we wanted to change it, and you were like, “Oh, that’s more work.” So, I think, ideally is you decide on a toe shape from the get-go and don’t change it.


[Simon] Right. Because like after the first kind of last is created, everything else is done by hand. So, we then, we had to build up the last to create a square-toe shape and do all the changes by hand, which is, also, which also works and is fine.
[Raphael] But of course, it’s that it’s cost-effective
[Simon] And also, it might kind of be a bit difficult to get the the same aesthetic, which that we were initially looking for.
[Raphael] Then, of course, if you use a computer, right? And you get the identical toe shape, versus if you do it by hand with a shoemaker, right, it’s… They get it close, but it’s obviously not identical because
[Simon] Exactly.
[Raphael] We’re humans and that’s that’s not possible. Cool, yeah. So, customization-wise, I felt like I could do a lot, maybe with my local shoemaker in St. Paul. I could maybe even a little more but yeah, I was positively surprised in what you could do. We could have also chosen, I think, a Norvegese welt, right?
[Simon] Yes.
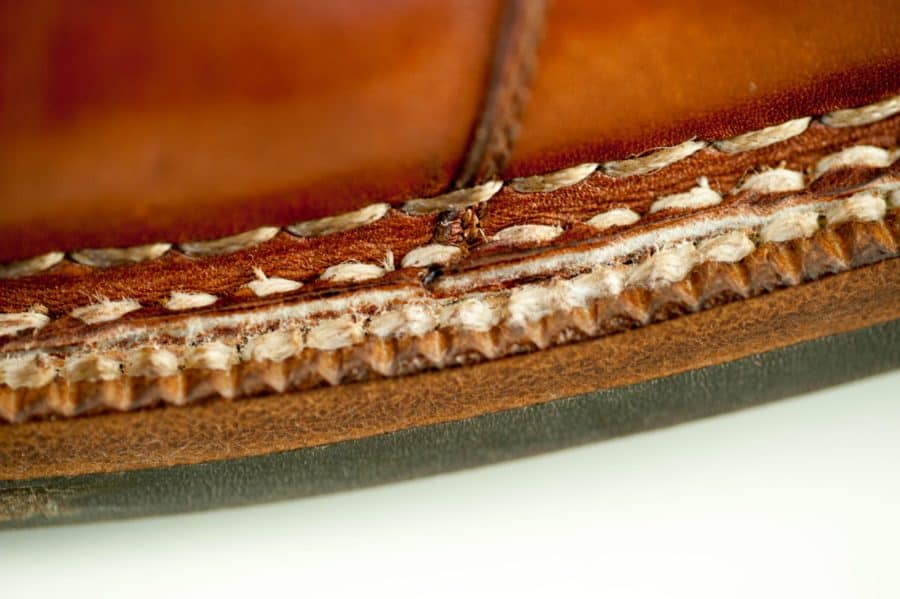
[Raphael] Yeah, you do those, and then do you also offer like wood peg here if people want it?
[Simon] No, we don’t do wood peg. What we do offer is that we put the initials with brass pegs in the waist.
[Raphael] But you can only do two initials, I think. Right?
[Simon] Yeah, otherwise, we’ll run out of space.
[Raphael] You run out of space, yeah. So, we just skipped that here and that’s totally fine but also, so like, if you maybe can pass the other shoe again. Does that have that you know, on your website you have these like Cuban style, and when I looked at it, I don’t know it seemed maybe a bit extreme to me. So, I asked him, “Hey, can you do something between a Cuban heel and like the normal heel that we have,” and were like, “Yeah, we can do that,” and I think it really kind of worked, right? This is a little higher.
Still nicely tapered on the side. Here, this is a slightly tapered to the front, right? So, you even can do things that are not on the website, so…

[Simon] That’s, yeah, that’s um I think like for the website in general, like the options we have, I try to slim it down a bit because most customers, they aren’t like us, and they love to go into every kind of detail and, so for them, I made it a bit easier to choose what what…
[Raphael] But like this, you can really see the difference, right? Like the angles and stuff, and oftentimes, like, having fewer options is easier for people. Otherwise, it’s just kind of paralysis of choice and nothing happens. So, from a business point of view, you’re like, “Well, it’s better if people actually have fewer choices,” but if you are one of those people who want a little more, you can do that.
[Simon] Yeah, you can always reach out to me and ask whether it’s possible or not. Oftentimes it is, and if it’s not, I will just tell you. But yeah, for the customer who orders his or her–mostly his–first pair of bespoke shoes, it’s easier to slim down the options and have a more streamlined process because otherwise, they will just be overwhelmed with all the options.
[Raphael] One thing I like to do is, if we look from the back, you can truly see, you know, it’s higher on the inside of the foot than on the outside; not something you get with a ready-to-wear shoe, even like high-end. That’s typical, done. I liked it very much. I appreciate that. Also, I think, if we compare these two here, I liked that I have a thicker, kind of folded over edge than having a pure cut edge. I, yeah, that’s something I requested and you were able to do.

The only thing that I saw that I thought was interesting was when we looked at the shoes here. Now, it came, and I noticed that you had a kind of cut edge here, right? So, I was like, “Well, why didn’t they put it like here where it was hidden underneath?” So, I didn’t quite get that. Was probably an oversight or something.
[Simon] Yeah. Good point.
[Raphael] Yeah ’cause I I noticed on this shoe, it’s it’s smooth all around, versus here, it it’s fine, right? And it’s a little detail it’s on the inside of the shoe. The pants are going to be over it. It was just something I noticed.
[Simon] Interesting.
[Raphael] And I was like, probably not many people notice like.
[Simon] Yeah, good point.
[Raphael] But uh, something I noticed but you know,I think it’s like with any bespoke product, right? The first shoe it’s … it’s almost impossible to get it 100% right, but in your case, though, I was I was impressed ’cause, you know, we got a trial shoe, I tried it on, and trial shoes are always very different, because even if you use kind of leather, which you do.
It’s, it’s not just like a, it’s a more kind of advanced trial shoe. It’s not the exact same thing, ’cause you don’t have to welt and the shoe looks different because you, this here like just looks very different. It’s much tighter, and then, the heel block, you know, is not like this. It’s kind of a square block, and it’s it’s like harder so you can walk around in those shoes, just to kind of feel how it feels, and then I took, what’s the usual step? You ask people to just put them on…
Trial Shoes: The Key to Perfect Bespoke Shoe Fit?
[Simon] Yes, and wear them for a couple of hours just in your home. The trial shoes aren’t really made to be worn outside. I mean, of course, for a little bit of time, but not for an extensive period. And then I asked them one, for one thing, like for the comments, like what kind of issues or maybe, aesthetically or also in terms of fit they find, have like a list with things they can go over and then for me, the most helpful is usually just some photos and videos, so you can just look myself.


I also work directly with my lastmaker, and we kind of together see what kind of things we would like to change. Also, of course, with the customer in mind, because fit is a very subjective thing, like everyone perceives a good fit a bit differently. So, some people like it when the shoes fit a bit more loosely, and some prefer it when it’s quite tight.
[Raphael] Yeah, you can ask, right? But people are like, “No I don’t like my shoes tight,” and then, you know you look at them, and you’re like, “Based on my experience levels, yes, you do.” You know, but it’s very subjective, so you have to work with a customer and figure it out, and I think with my shoe, I like it like we did that and you gave us very specific instructions on how to cut them open, and, you know, we use our cameras to film it, but obviously, you can just do phone footage. It’s so good these days, it really helps, and being remote, it’s just important having that extra detail, because you can’t be there in person.
But then, I think you made another trial shoe based on that initial feedback, and um, that’s your standard process, right you do two trial shoes, kind of one, depending on how…
[Simon] Depends, yeah. Standard is one, but of course, there are some cases where two trial shoes are needed. In very rare cases, also three. But we usually don’t go to the finished product if we aren’t comfortable with kind of where the shoes are at.

[Raphael] ‘Cause you want people to be able to wear them even if they’re not 100%, you know? You get 95%, 98% there.
[Simon] Exactly. Exactly.
[Raphael] Okay, and I think in my case, there was because we had that foam layer … it was kind of funny because, I, the first shoe came with a foam layer, and the second one didn’t have it. So, actually, fit really differently. I was like, I think that’s the reason, and then I changed it, and I put it in.
But I could remember I could feel it, you know, on my ankle joint, on the outside but then that the final shoe was different. It was good. But obviously, it’s yeah, you think because you use a leather material, the trial shoe is just like the real shoe, but it’s not. The way feels and stuff, it’s not, but it would be too expensive. I mean, part of the reasons you go, most people go, remote bespoke is because you have an attractive price.
[Simon] Exactly.
[Raphael] So, we’re talking about the starting price of…
[Simon] 1300-1500 euros. For first-time customers, it’s a bit more expensive because you have to pay for the initial last and the fitting shoes. But then, yeah.

[Raphael] And you have different options to even, you can have like a hand-sewn welt. Do you… I think you also have a Goodyear option, is that right?
[Simon] Uh, no. So, all the standard option is that the waist is sewn by hand, and the outsole is sewn by machine.
[Raphael] Just show us.
[Simon] So this part, which is like very tight, and you you can’t see any stitching, actually. It is all done by hand and then from here onwards, it’s done by machine but still very very tight, and a very close stitch density. But we also offer an option where like, all around is done by hand, which, of course, some people like who are very, like purists and and enthusiasts, love to choose but generally, people are fine with this because you don’t really notice that much of a difference at that point.
[Raphael] Yeah, it’s not visible, but you can bring the price down that way.
[Simon] Exactly.
[Raphael] Then you also offer shoe trees; is that included by default, or is it an upcharge?
[Simon]That’s an upcharge. So, depending on the model, these are the kind of… They’re always lasted, of course. They’re made to your, like it’s essentially a copy of your bespoke last. We have a couple of different options for the shoe trees, and that kind of depends also on the price, but we also try to be less expensive than traditional makers.


[Raphael] Yeah. So, this is like, what is it? Oak? Looks like…
[Simon] I think it’s sandalwood.
[Raphael] Sandalwood, maybe. okay. Okay. Um, yeah. I mean, I think if you go the extra mile of a bespoke shoe made it’s in the cost-per-wear interest to get the lasted tree. It’s so much better, so I, like, if you go this route, definitely add them in. I think yeah if this down here was a little more rounded or just taken away, I think it would be even better… because then I could put them in more easily and stretch them and it wouldn’t hurt the shape of the shoe ’cause if I’m not having that extra, if I have more negative space, I think it would be easier to put them in, and there wouldn’t be no discernable leftover.
[Simon] Yeah, so the shoe trees are the only thing we don’t do ourselves.
Belts & Shoe Trees: The Perfect Partners for Bespoke Shoes
[Raphael] Okay.
[Simon] I work with a factory in Spain, but probably will work with a different company in the future. So, this is something we are kind of trying to work on.
[Raphael] And that’s normal with any company, right? You have a vendor, and then maybe they are not, they don’t do what they say they do, and you’ll move on or you change things. It’s a very normal process with anyone who offers products. Okay, nice. So yeah then I mean once you are confident with the fit you’ll basically make the shoes, right? So, how long does it normally take from, you know, the stage customer reaches out and expresses interest, and then or, let’s say customer commits, right? So, you just make a down payment you make a payment in full?
[Simon] Make a payment in full, and then we create the last, we make the fitting shoes. The fitting shoes, as you mentioned, we try to be as close to the finished pair as possible, so we make actually the full pattern, not just like, some shoemakers do just a generic Oxford or whatever. We try to do the actual pair that was ordered for the fittings and yeah, so the fitting shoe to be made with the last and so on takes around four weeks.

So, after 4 weeks, we can send out the trial shoes to the customer, and then it always depends a bit on the customer how fast they kind of respond, how fast they kind of push, put, push the process forward, but once I have all the feedback I need and we’re comfortable to go to the finished pair, it usually takes around 10 to 12 weeks for the actual pair to be made, which is also a bit faster than traditional makers, which often have like a big backlog of orders and so on. So, yeah.
[Raphael] So, that’s quite a good time frame. I mean, there can always be delays, right? With COVID and things, like it’s not within you, so I think, you know, if you have a deadline like a wedding and you need it by then, I’m like I wouldn’t bet on that. It’s like, give yourself a little more time.
[Simon] Yeah, exactly.
[Raphael] Just so it can actually work and be successful, ’cause the last thing you want to do is, like, rush it and maybe feel like you’re pushing it through just because you need it by that specific date
[Simon] Yeah, I think most customers ordering bespoke are used to kind of the process taking a bit more time usually, when they buy bespoke shoes from us, they usually have already made some experiences with maybe ordering a tailoring bespoke. So, they know things can take their time. So, usually, they aren’t in a rush, and if I have customers who need it for their wedding, which I’ve also had, they usually reach out like within one year in advance.
[Raphael] That’s great.
[Simon] There’s sufficient time to get things right.
[Raphael] That’s great. Nice. So, can a customer supply their leather? ‘Cause I think I saw like @mr.renworks on Instagram, right? Like, he had this really cool shoe. It was like, was it alligator?
[Simon] It’s a caiman. Yeah.
Why Are Crocodile & Alligator Leather Goods So Expensive?
[Raphael] Caiman? It was this like reverse, it was this really cool effect. You did a really nice job on the patina. So, one thing that so, maybe not so obvious, ’cause most people don’t choose it, but you offer really stunning patina options, right?


[Simon] Yeah, that’s also something we do. We can also make the shoes in a cross calf, which is like an undyed calf, and then we do a hand patina. So, hand-painted patina on it, in pretty much any color or shade you want. Of course, with that, expectations have to be managed because it won’t look exactly like this, the same as you, maybe the example picture you will show us, but we try to get as close to it as possible.
[Raphael] Yeah, no, but it’s pretty impressive and just like with art, right, you getting the exact copy, some, sometimes different people have different ideas. There are marble effects. I mean, there’s so much out there, but your people can do pretty good stuff. So, I thought it was quite impressive. Overall, I think, the outcome of my first shoe, it was good. I think probably the foam threw things a little bit off. I have these very kind of tight heels, and we talked about it a few times. I think they probably could have been a little tighter, but to be fair, I had that same thing, that same issue happening with the bespoke shoemaker I worked with in person.
[Simon] Mhm, okay.
[Raphael] So, with Amara, the first could be a little tighter into the heel, and loafers are also hard for a first shoe. They are, I mean, loafers in general. I think people don’t realize it, but a lot of bespoke shoemakers don’t like doing loafers because you need an entirely new last, right? It’s similar to maybe like a Chelsea boot, I think. So, I’m always like, okay, if you want, if you like Chelsea boots, that’s great to go with bespoke or a loafer, ’cause they have to stand your foot, you can’t compensate with the laces.
[Simon] Exactly.
So, that [loafer] is definitely trickier. I definitely threw the trickiest option at you that was possible.
SVEN RAPHAEL SCHNEIDER
[Simon] Yeah.
[Raphael] And actually, I’m going to put them on now, so you can kind of see what they’re like, because that’s the first time. That’s obviously, you can’t see it. You can see a video of maybe what the final shoe looks like on a person, but then, like the second pair should be really really good because there’s no issue in making adjustments.

[Simon] Yeah, and also, like, even when you get the shoes new, and once they’re broken in the fit will be very different and that’s something you can’t really kind of predict in advance, so it always makes sense, once you have your first pair that you break in the shoes for a couple weeks, and see kind of some issues, which you might have at first, they kind of disappear, but maybe other things that aren’t perfect will appear after, just after a few weeks. So, it makes sense to break in the shoes properly before we make any adjustments
[Raphael] So, you’d say break-in period, how long?
[Simon] I mean, of course, it depends on how much you wear the shoes, but usually, you will feel it once the shoes kind of molded to your foot a bit more.
[Raphael] So, what if I wear them like, you know, if I walk like two hours a day. Like two weeks, 3 weeks?
[Simon] Probably, yeah, like 5 to 10 wears probably is enough for it to kind of, to see what the actual wear looks like.
[Raphael] Nice. Okay. Well, let’s, actually, like I’ll put them on here and you just share your feedback, what you want. So, overall, what’s, how, what do you… I see more like wrinkling here. Is that part of the leather, you think? It’s, you’re just more likely to, I mean there’s always some amount of wrinkling. You’re not going to avoid that.

[Simon] So, you need a little bit of space for the wrinkles to go somewhere. You don’t want it to be completely close-fitting.
[Raphael] Yeah.
[Simon] Of course, as close as possible, but you need some wrinkles are kind of normal, because the leather needs to go somewhere. Also, the leather you chose is a bit more difficult because it’s a bit thicker, it also makes it a bit more difficult to put shape in, into the toe shape, for example. If it was like just a regular calf, it would look a bit more refined even than this.
[Raphael] Yeah, that’s true and it’s it’s a grain calf, and I mean, can you split the leather to your desired thickness, or do you basically get it like that from the tanner?
[Simon] We usually get it like this, yeah.
[Raphael] So overall, I think it’ll get, yeah, as I wear them more, I’ll see how they break in, but I’m, you, know very happy with the way it turned out, considering it is remote.
[Simon] Yeah.

[Raphael] And yeah, I think it’s a really good first option if you’re new to it, you want to check it out, especially if you live in an area where there’s no bespoke shoemaker.
[Simon] Exactly. That was kind of the idea behind it and that’s also the majority of customers I get; from mostly US customers, like from rather remote areas usually, and also in Asia. So, it’s quite an interesting offering, I think.
[Raphael] Yeah, I still, I think it’s it’s not even an either or, you know. I have a bespoke maker in my hometown, and I love the relationship with her, I love being able to work on things like, you know, we’re working on an alligator loafer right now, so alligator, for example, would be difficult with you because if I wanted to ship like there’s that CITES regulation. So, doing it for a single pair of something is just crazy burdensome paperwork and all that stuff, right? The import costs you thousands of dollars. So, I think that just wouldn’t make sense, right?
So, that’s the use case where I’m like, go with someone on your continent, so you don’t have to send it across borders, for example, right? Special things like that or like we were even like, you know, discussing. “Okay, this is the pattern,” and before, you know, she cuts it, we’re looking exactly on a particular skin how it’s going to be cut, so we make sure everything is the way, you know, we want it, and I’m obviously more detail-oriented than the average person so that comes into play as well.
How Uppers Are Designed & Cut for Bespoke Dress Shoes
But, yeah, I think, you know, being able to get that lower price point and doing it without actually putting in much time is really worth it. For all of our bespoke projects, you have to travel somewhere, and then that is cost, that is extra time. And yes, you can make it a vacation or something, but it’s different. So, I think, yeah, the pros are really: it’s a low price, relatively speaking.

[Simon] Relatively, yeah. It’s not cheap, but uh…
[Raphael] It is, you get a nice product. It’s a quality product.
[Simon] I think so, yeah.
[Raphael] You can truly kind of yeah customize it. You also, you’re not pressured, right? When you’re like at the shoemaker, and maybe you forget something, you have all the time in the world, and if it comes back to you, you can take your time and think, get over through a day to get that…
[Simon] Yeah, exactly.
[Raphael] That right idea that you have in mind.
[Simon] Yeah, yeah. I think so, too.
[Raphael] I think that is very helpful. Yeah, it really, I like that you made bespoke shoes accessible to a lot of people that previously wouldn’t have able to afford it either because of the travel cost, or the overall cost. So, yeah, thank you for what you do, Simon. I appreciate you.
[Simon] Thank you for having me.
Visit the Wayman Bespoke website!
If they were made in any other country then China, I would consider buying their shoes. I have a small foot and there are Italian shoes but they want to put patina on the shoes which I do not want. I ask them not to put the patina on the shoes but they said the can not do that. Try doing what Apple did with the iPad and made them in Vietnam.
What makes you say that the shoes being made in China is a detractor for you? Equally, why is Vietnam a better place to make bespoke shoes in your view?
I agree with Douglas…I am totally turned off by anything made in China as they exploit their workers PERIOD
I agree with “Douglas” putting a “patina” on shoes when you specifically don’t want it, tells me something is not right with the leather itself. If you have to add “color” to leather than I don’t want anything to do with thoes shoes.
Bespoke or not, keep them!
As Simon discusses in the interview, the patina service is an option, not a given. Even traditional shoe colours such as black and tones of brown are added to the leather, which is naturally closer to white in it’s raw form. That being said, the customer has the control in the Wayman Bespoke process, so you can pick whichever colour/type of leather you see fit.
Hello Jack, yes I realize that shoes are “dyed” different colors to make the shoes look better, however adding a “patina” when the customer specifically asked not to as “Douglas” did not want it tells me that they don’t care or there is something else that they are doing.
Either way I stand by my reply.
Why should I purchase from them?
Not for me!
Hi Richard,
If I understand correctly, Douglas is talking about an Italian shoemaker not us in regards to the patina. We use the box calf, suede, grained calf etc. from the same tanneries (Haas, Ilcea, Horween, CF Stead, etc.) as any other bespoke shoemaker in Europe and I source them here locally. Not only the uppers, but also insoles, outsoles, stiffeners and so on. We only dye the shoes a certain color/ add a patina if the customer requests it, which is quite rare. For this we usually use and undyed crust calf, where defects etc. would be even more visible.
Hope that clears things up!
Best,
Simon